コスト・加工時間を低減する方法
(サイドカッターの刃先の折損を減らす)
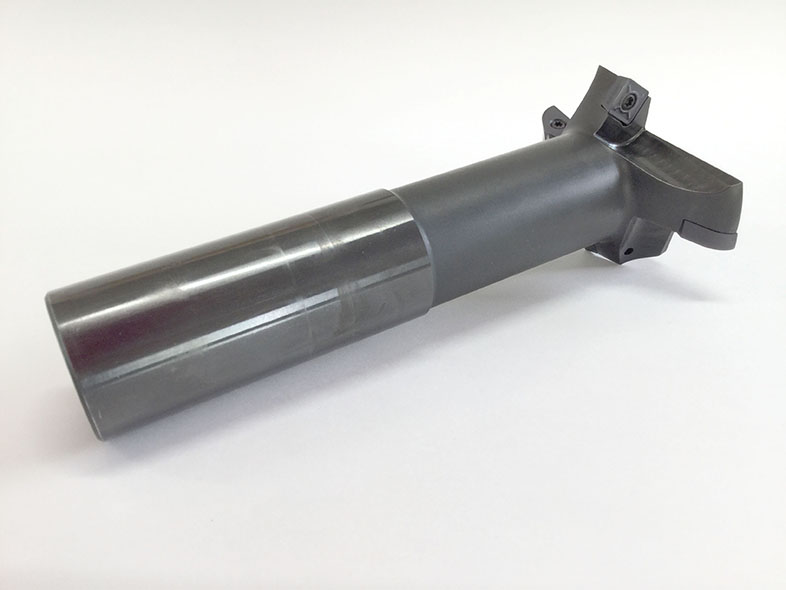
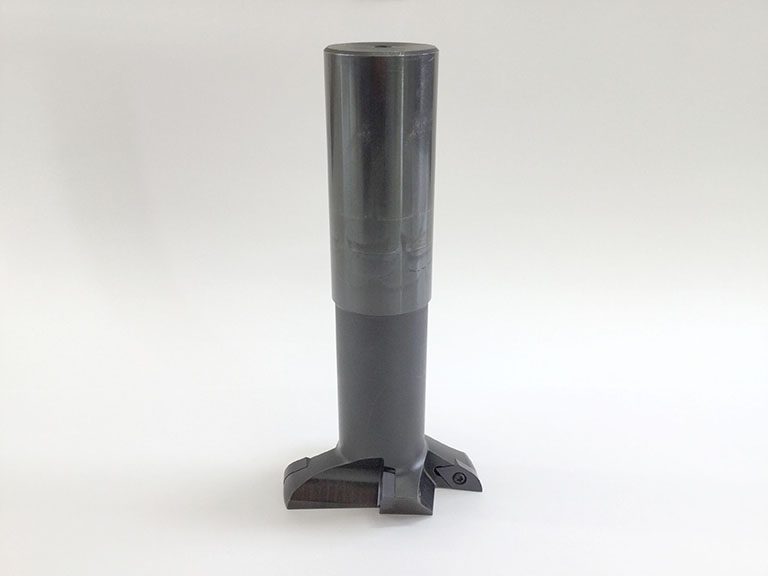
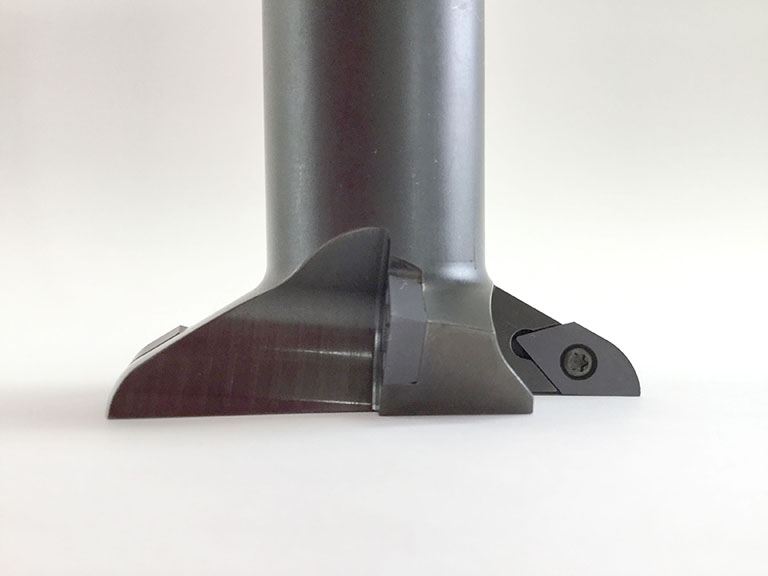
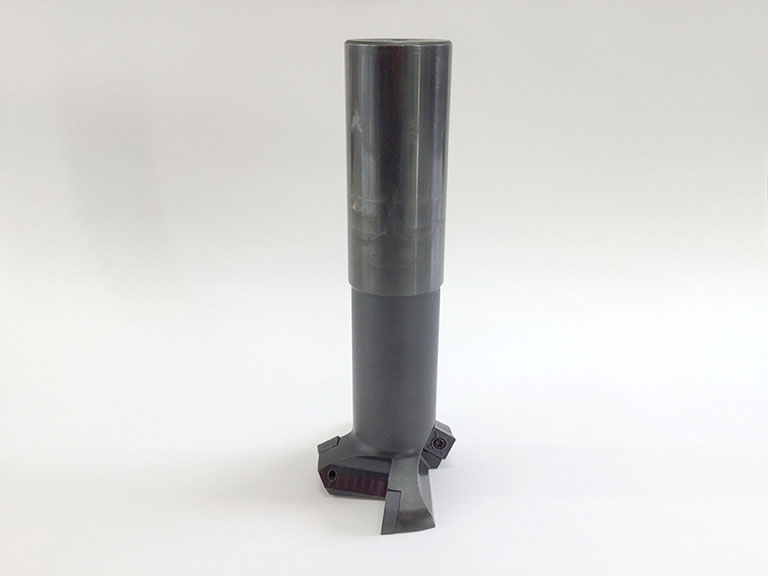
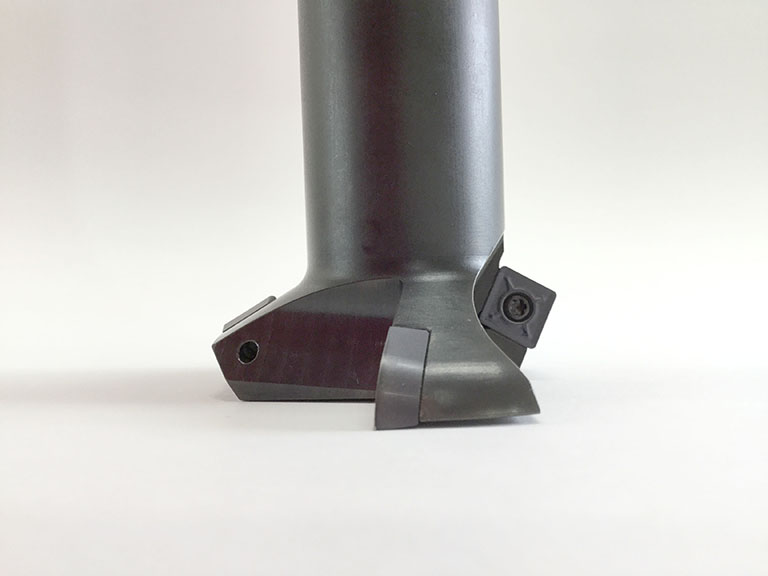
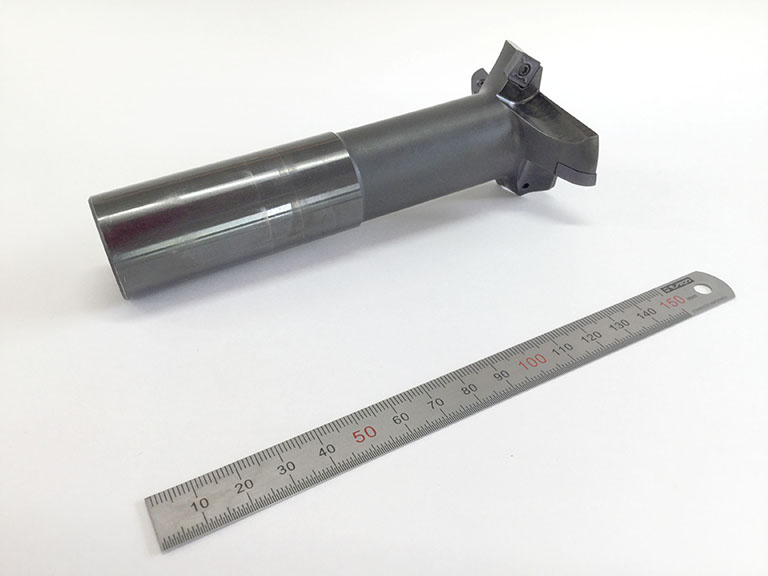
-
お客様の課題・リクエスト
特殊形状の開先加工時、コスト低減・加工時間削減のために何かアイデアはないか。
-
提案内容
『開先加工』とは、溶接部分の強度を保ち、尚且つしっかりと密着させるため、溶接する対象物の縁を切り開くことをいいます。開先の形状には,I形,V形,X形など色々あります。しかし、開先形状が複雑であればあるほど、加工が難しくなり、工数管理も厳しくなります。
そこで、開先形状に合わせた超硬サイドカッターを製作(メーカー特注)しました。
これにより、工具費は1/5に低減、加工時間も1/3に低減しました。
特殊開先形状の加工の場合、従来はハイス製のサイドカッターを使用していましたが、切粉詰まりによる刃先の折損が多く、折損の度、サイドカッターを新規製作していました。
また、物の大きさにもよりますが、多いときには一つの製品につき2~3回折損を起こすので、作業の妨げになったり、コスト面に於いても割高になる傾向がありました。
これを改善すれば、コスト低減および加工時間削減に繋がると考えました。これが特殊工具を製作した経緯です。
-
製品特徴
難削材を一気に切削すると、折損しやすくなります。
そこで、
・どんな刃先なら折損しにくいか
・サイドカッターをどのくらいのスピードで動かすか
・削り方をどうするか
など、長年の経験と知恵を基に、改良に改良を重ねた結果、下の写真のようなサイドカッターの形状になりました。
写真をよく見るとお分かりの通り、刃先が4つに分かれていて、それぞれ形状・大きさが少しずつ違います。
例として、このサイドカッターを使用し【図③】のように削るとします。
一気に削らず、削り方を変えながら【図④】のように少しずつ削っていきます。
このように、開先形状に合わせて削るスピードや角度・刃先を変えながら少しずつ削っていきます。 -
営業担当からのコメント
特殊工具を開発する前は、サイドカッターの刃先の折損のたびにサイドカッターを交換し製品を作っていました。
そのため工具費が嵩むうえ、サイドカッターの交換のために作業を一時的に止める必要がありました。
そうなると加工時間も増えるため、お客様の『出来るだけ早く欲しい』というご要望に添えない場合がありました。
そこで、《上記写真》のように、開先形状に合わせた超硬サイドカッターを開発することで、工具費は1/5に低減、加工費も1/3に低減することが可能となりました。
サイドカッターの先端をどのような形状にすれば折損しにくいか、試行錯誤を繰り返して出来た工具です。